Planning Pays Off: 5 Strategies to Get the Most Out of Your Delivery Speed Choice
September 26, 2024
5 min read
Introduction
There are more than 26.6 million eCommerce stores globally. In 2024, 20.1% of retail purchases are expected to occur online, and this share will rise to 22.6% by 2027.
The order management process is gaining momentum in this competitive market to improve customer retention and loyalty. Effective order management includes placing orders to deliver products, including coordinated picking, packing, and shipping. Returns also form part of this process.
The order management process involves several teams and their coordination with different systems. Enhancing the order management process will improve efficiency and customer satisfaction.
This guide revolves around how order management could be enhanced with ease.
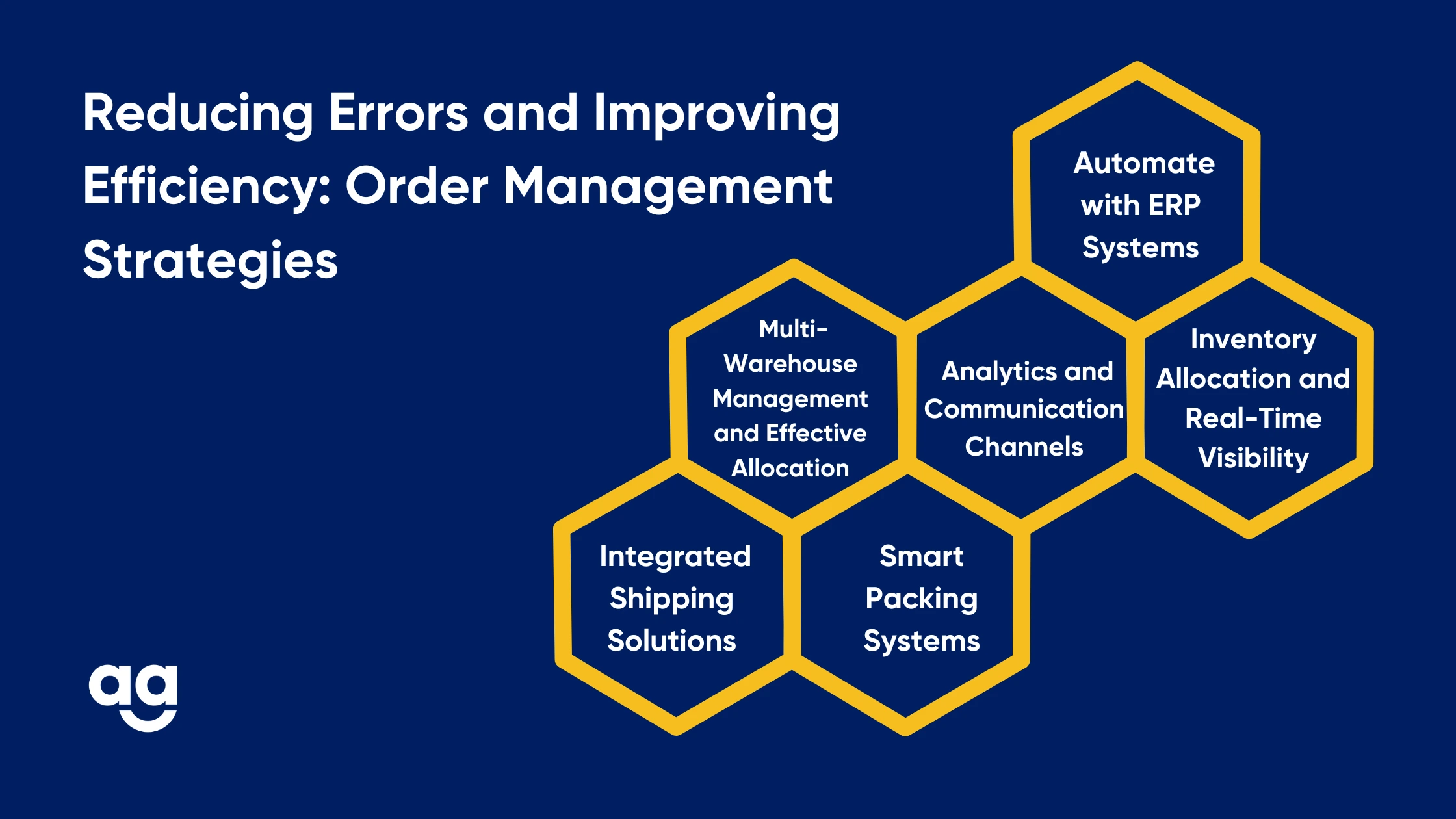
How to Effectively Process Order Management
Order management means processing the customer’s order from its placement until delivery. It helps minimize errors while enhancing customer satisfaction through better workflow efficiencies and improved inventory management.
Over 80% of online shoppers expect real-time order updates, while 70% claim they would purchase again from companies offering real-time, transparent tracking, and rapid deliveries.
77% of online shoppers reported expecting their orders to be delivered within two hours or less.
Efficiency in the order management process empowers organizations and helps them meet customer expectations.
6 Order Management Strategies that Reduce Errors and Increase Productivity
Effective order management is about delivering outstanding customer experiences while managing operational costs and resource utilization. Here are key strategies that will enhance order management:
Automate with ERP Systems
Automation replaces human manipulation. This helps in reducing errors and increasing efficiency. This is where an ERP solution is helpful, as it assists in automating these processes and forecasts. It further helps in:
- Tracking orders
- Customer relationship management
- Improving productivity and revenues
Inventory Allocation and Real-Time Visibility
Accurate inventory allocation can avoid stockout situations and overstocking. Inventory visibility in real-time can enable the following:
- Allocating the product correctly across various sales channels
- Managing real-time inventory management systems
- Helping businesses with stock allocation
- Avoiding delays and incompleteness of orders
Analytics and Communication Channels
ERP systems come with valuable analytics that help decision-making processes and forecast inventories. This information should be communicated to employees, and they should be trained to adapt to newer technologies.
The whole supply chain becomes much more effective and transparent in the process.
Multi-Warehouse Management and Effective Allocation
Businesses operating several warehouses must assign orders to the right warehouse or fulfillment center. This reduces shipping times and ultimately cuts costs.
Companies can manage warehouse allocations based on various factors:
- Proximity to customers
- Inventory levels
- Operational efficiency
- Peak season demand, and so on
Smart Packing Systems
The packing process is important to ensure the correct delivery and arrival of orders. Advanced packing systems integrated with order management platforms can streamline the process of packing in the following ways:
- Auto-instruction generation
- Printing of shipping labels
- Compliance with carrier requirements
- Packing stations can be more efficient with adjustable surfaces and easy access to materials like bubble wrap and boxes.
- Standardizing packaging allows for much better efficiency, as fragile or sensitive items are secured well enough not to get damaged during transit.
Integrated Shipping Solutions
Shipping is quite an integral part of the fulfillment, and integrating your order management system with shipping platforms may speed things up. Businesses can cut down on time spent on order processing and reduce manual errors by:
- Automated label printing
- Generation of customs forms for international shipments
- Meeting the regulations for quick processing
Conclusion
Order management strategies mean managing an order for higher customer satisfaction, operational efficiency, and growth. It is all about being aware of every critical stage associated with order type, channel, and workflow and how best to adjust the strategy to fit business needs.
By utilizing advanced tools and practices, businesses can be rest assured that their operations flow without glitches and that there are minimum errors, which in turn helps reach the ultimate goal of customer satisfaction.
Collaborate with leading international courier services like Shipyaari to understand how integral order management strategies can improve your CX.
You can also use services like Shipyaari Delta that offer automated WhatsApp communications for real-time updates.
Frequently Asked Questions
Effective order management extracts these three essential elements: process optimization, data visibility, and system integration.
Common mistakes in order fulfillment are made by:
- Picking incorrect or damaged products
- Bad inventory control
- Low capacity in the warehouse
- Failure to automate processes
- Inability to manage customer returns
Best practices for minimizing errors in a business’s packing include standardizing packaging and verifying packages.
Packing stations must be equipped with tools, and the staff should be given clear work documentation. This may also involve a strict quality assurance process, using automation to enhance speed and accuracy for much smoother operations.
Suggested Reads
Hyperlocal Personalization: Tailoring Experiences for Local Customers
Introduction The eCommerce industry in India has witnessed a rapid growth of hyperlocal services in
Continue ReadingDec